A joint cross-company development project between groninger and SKAN resulted in a unique line concept for vial processing – called integra. The integra product family is a sophisticated line concept integrating both isolators and filling machines which revolutionizes the pharmaceutical industry. This joint vision of groninger and SKAN could be realized in a very short time and includes different lines offering top speeds and standardized isolator technology. The integra filling line is the latest member of the groninger and SKAN business line.
Key data of the integra isolator system
- The isolator has EU GMP Class A (ISO 5) production chamber for highest product protection.
- integra offers highest safety for operators as well as for the whole process.
- The integrated skanfog® technology allows fastest decontamination cycles.
- A new, exclusive cleaning validation process is used.
- The isolator system offers unique ease of operation and ultra-slim machine design.
- integra allows optimal access to operate the entire line from only one side.
- The isolator is suitable for aseptic and highly potent/toxic products.
Get in touch with our sales team!
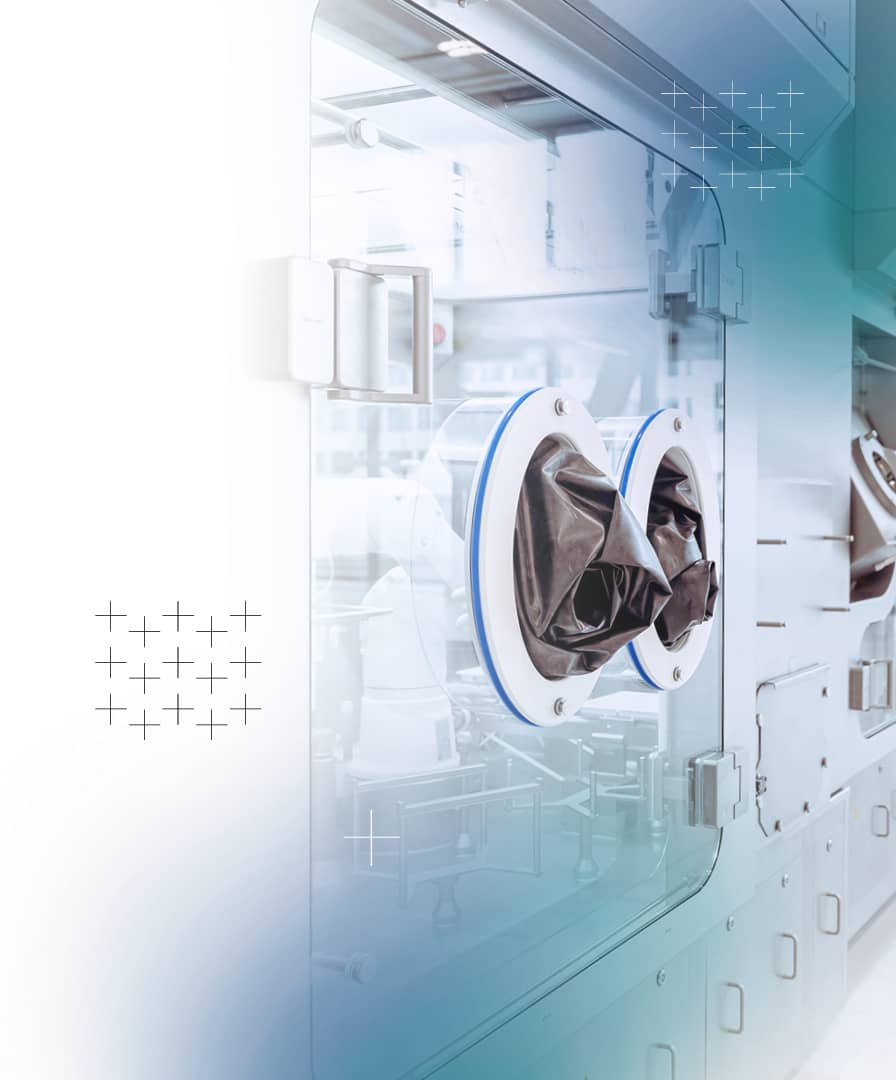
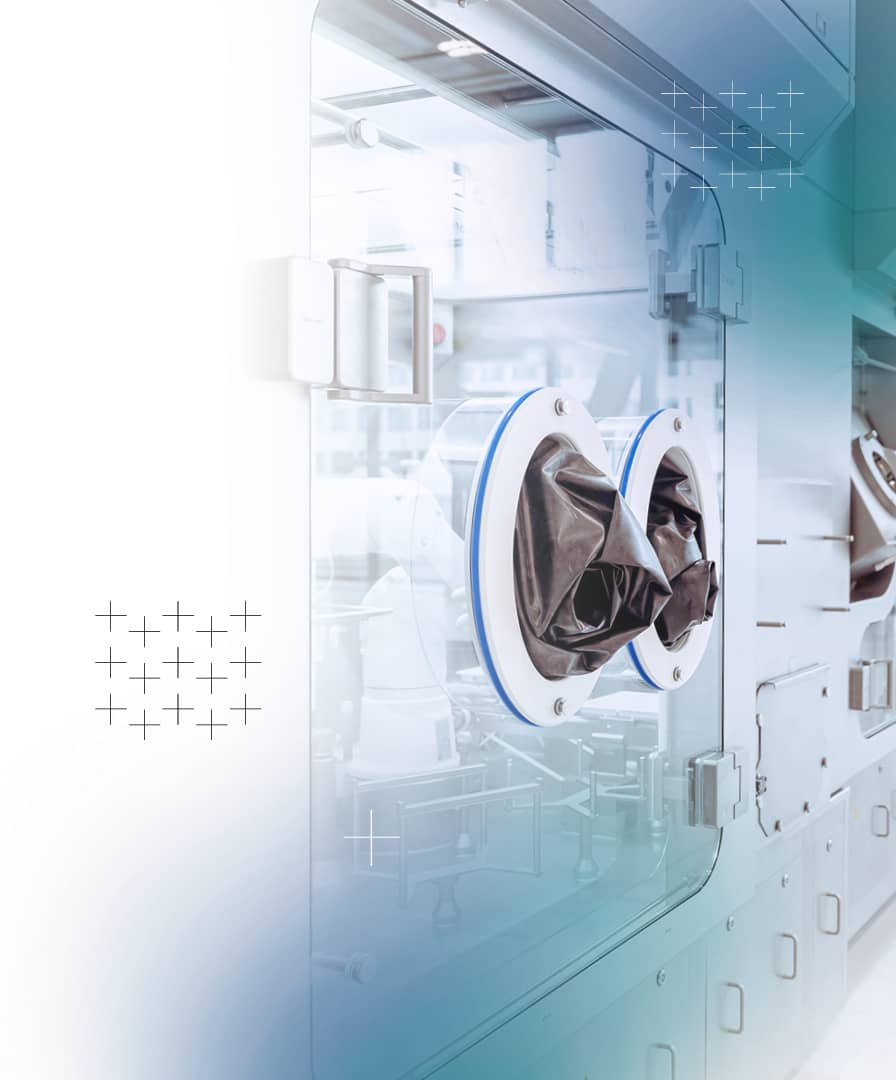
integra partner
groninger designs and manufactures machines for the processing of pharmaceutical and cosmetic products. The core competency of groninger, founded by Horst Groninger in 1980, are technological solutions for filling and closing pharmaceutical containers such as syringes, vials or cartridges. Above that, groninger builds machines for the the consumer healthcare and cosmetics industry. groninger currently employs over 1500 people at the two German locations Crailsheim and Schnelldorf and in Charlotte (North Carolina, USA).