The pharmaceutical industry has undergone significant changes in recent years. While blockbuster drugs used to dominate, the focus is now on patient-specific solutions, requiring smaller batches and shorter time-to-market.
The robocell was specifically designed to meet these new challenges. Developed in collaboration with groninger, this gloveless filling line automates all processes within the aseptic core, delivering maximum safety, flexibility, and efficiency while adhering to the strictest regulations, such as Annex 1.
Why choose robocell?
- Maximum sterility assurance by eliminating human intervention
- High automation level for reproducible and robust processes
- Full compliance with Annex 1
- Flexibility in product and container selection
- Minimization of product loss
- Maximum efficiency through rapid format changes
Get in touch with our sales team!
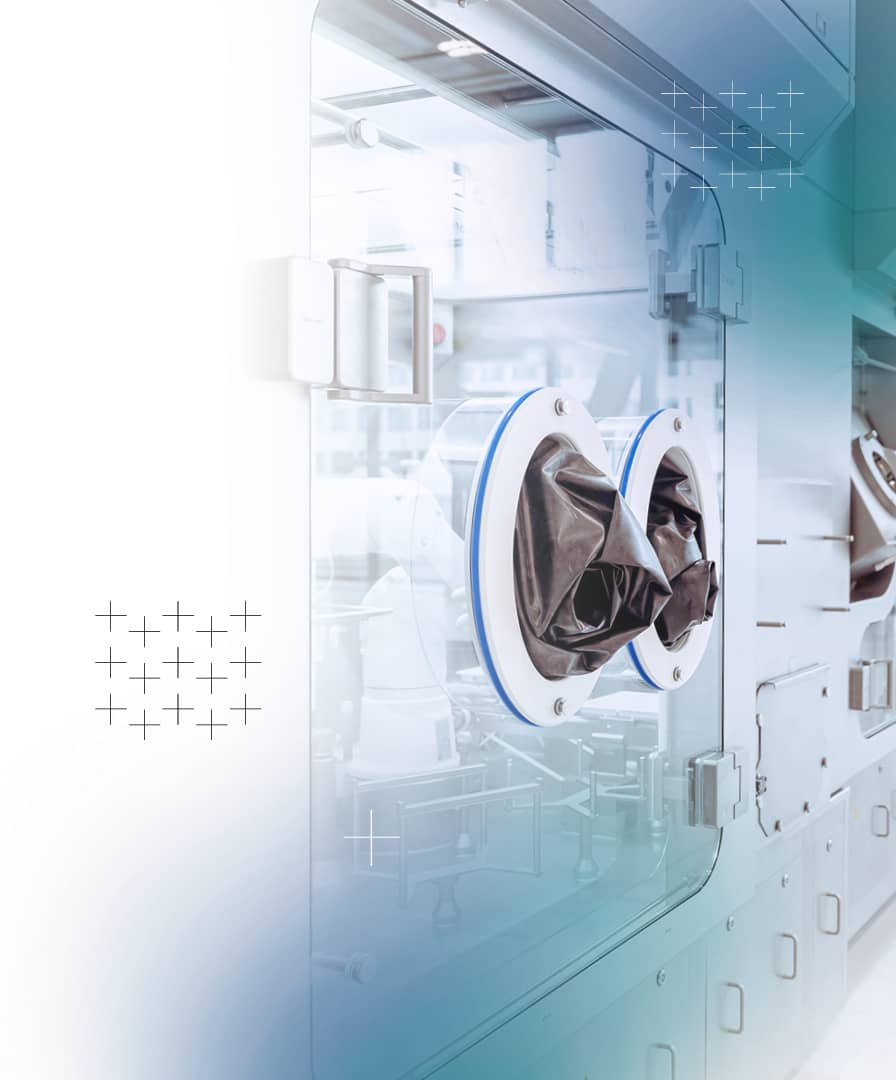
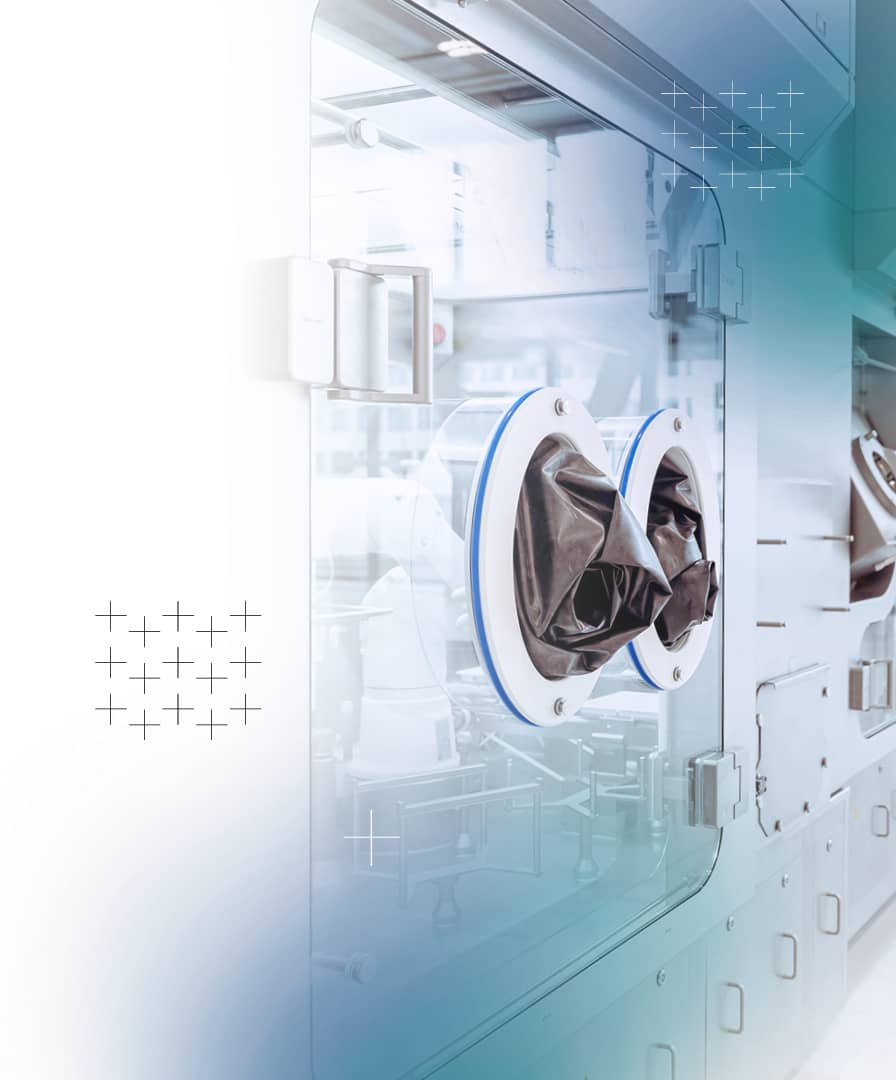
robocell partner
groninger designs and manufactures machines for the processing of pharmaceutical and cosmetic products. The core competency of groninger, founded by Horst Groninger in 1980, are technological solutions for filling and closing pharmaceutical containers such as syringes, vials or cartridges. Above that, groninger builds machines for the the consumer healthcare and cosmetics industry. groninger currently employs over 1500 people at the two German locations Crailsheim and Schnelldorf and in Charlotte (North Carolina, USA).